Our company has a very organized and effective work methodology thanks to the experience of our workers and the years developing projects and works carried out.
Below, we explain in detail the step by step:
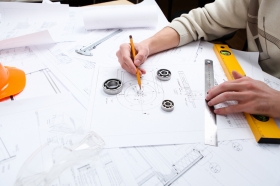
Our company has a very organized and effective work methodology thanks to the experience of our workers and the years developing projects and works carried out.
Below, we explain in detail the step by step:
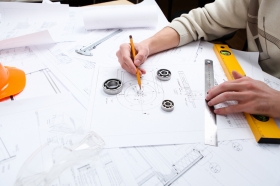
Our company has a very organized and effective work methodology thanks to the experience of our workers and the years developing projects and works carried out.
Below, we explain in detail the step by step:
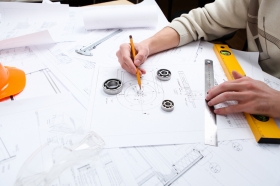
Since each project is different due to its unique and specific characteristics, a detailed study of each project is carried out in order to finally present the most adequate budget for each particular project.
Our technical staff, with sufficient training and experience in the reading of blueprints, develop the cutting sheets with the help of a specific computer program for this purpose. This program generates the cutting sheets and labels, which will later be sent to the workshop where they will be cut, folded and assembled according to the established order of preference.
The Workshop Manager is the person in charge of ordering the execution of the templates and supervising both the elaboration process and the final product.
The steel is cut on the so-called cutting line and then bent, when necessary, and reinforced.
In the bending and fabrication of stirrups, state-of-the-art machinery is used to optimize both bending lengths and angles, thus obtaining a perfect finish in bars and stirrups.
The placement of stirrups is done automatically by the jointer, thus achieving an exact separation of the stirrups.
In this way, the quality of the reinforcement is far superior to the manual ones, welding any stirrup, regardless of its shape, by means of three small longitudinal wires placed on the outside. The structure thus formed is finished with the insertion of the bars inside the reinforcement and their fixation by semi-automatic welding and/or steel wire, in both cases, three stirrups are left loose at the ends to facilitate their placement on site.
Finally, the negatives and positives that make up the element are checked and its identification label is placed so that, once on site, there is no problem to know in which position it is placed.
When we have a complete order of sheets finished, they are stored in the workshop for later loading and delivery to the construction site.
After planning the shipments to the site, adapted to the supply rhythm set by our customers and to the unloading schedules, our trucks are in charge of delivering the iron.
All the raw material used in our products (corrugated iron) has the AENOR quality seal, in order to certify the competitiveness of our products in the market.
Since each project is different due to its unique and specific characteristics, a detailed study of each project is carried out in order to finally present the most adequate budget for each particular project.
Our technical staff, with sufficient training and experience in the reading of blueprints, develop the cutting sheets with the help of a specific computer program for this purpose. This program generates the cutting sheets and labels, which will later be sent to the workshop where they will be cut, folded and assembled according to the established order of preference.
The Workshop Manager is the person in charge of ordering the execution of the templates and supervising both the elaboration process and the final product.
The steel is cut on the so-called cutting line and then bent, when necessary, and reinforced.
In the bending and fabrication of stirrups, state-of-the-art machinery is used to optimize both bending lengths and angles, thus obtaining a perfect finish in bars and stirrups.
The placement of stirrups is done automatically by the jointer, thus achieving an exact separation of the stirrups.
In this way, the quality of the reinforcement is far superior to the manual ones, welding any stirrup, regardless of its shape, by means of three small longitudinal wires placed on the outside. The structure thus formed is finished with the insertion of the bars inside the reinforcement and their fixation by semi-automatic welding and/or steel wire, in both cases, three stirrups are left loose at the ends to facilitate their placement on site.
Finally, the negatives and positives that form the element are checked and its identification label is placed so that, once on site, there is no problem to know in which position it is placed.
When we have a complete order of sheets finished, they are stored in the workshop for later loading and delivery to the construction site.
After planning the shipments to the site, adapted to the supply rhythm set by our customers and to the unloading schedules, our trucks are in charge of delivering the iron.
All the raw material used in our products (corrugated iron) has the AENOR quality seal, in order to certify the competitiveness of our products in the market.
Since each project is different due to its unique and specific characteristics, a detailed study of each project is carried out in order to finally present the most adequate budget for each particular project.
Our technical staff, with sufficient training and experience in the reading of blueprints, develop the cutting sheets with the help of a specific computer program for this purpose. This program generates the cutting sheets and labels, which will later be sent to the workshop where they will be cut, folded and assembled according to the established order of preference.
The Workshop Manager is the person in charge of ordering the execution of the templates and supervising both the elaboration process and the final product.
The steel is cut on the so-called cutting line and then bent, when necessary, and reinforced.
In the bending and fabrication of stirrups, state-of-the-art machinery is used to optimize both bending lengths and angles, thus obtaining a perfect finish in bars and stirrups.
The placement of stirrups is done automatically by the jointer, thus achieving an exact separation of the stirrups.
In this way, the quality of the reinforcement is far superior to the manual ones, welding any stirrup, regardless of its shape, by means of three small longitudinal wires placed on the outside. The structure thus formed is finished with the insertion of the bars inside the reinforcement and their fixation by semi-automatic welding and/or steel wire, in both cases, three stirrups are left loose at the ends to facilitate their placement on site.
Finally, the negatives and positives that form the element are checked and its identification label is placed so that, once on site, there is no problem to know in which position it is placed.
When we have a complete order of sheets finished, they are stored in the workshop for later loading and delivery to the construction site.
After planning the shipments to the site, adapted to the supply rhythm set by our customers and to the unloading schedules, our trucks are in charge of delivering the iron.
All the raw material used in our products (corrugated iron) has the AENOR quality seal, in order to certify the competitiveness of our products in the market.